Pour augmenter l'efficacité logistique, Bus Industrial Tools a décidé de centraliser son stockage de matériel. En 2016, ils ont donc construit un nouveau centre logistique à Zwolle. Tous les matériaux seraient collectés ici afin qu'il ne devrait pas y avoir un grand stock dans les magasins séparés.
Les commandes passées avant 16 h sont livrées au client le lendemain. Pour ce faire, ils ont immédiatement cherché des opportunités d'automatiser une partie de leur nouvel magasin. Finalement, Bus a opté pour une solution globale dans laquelle les convoyeurs à rouleaux, les tours de stockage, des rayonnages et des armoires à tiroirs ont été combinés. Ils l'ont fait en collaboration avec Vanas Engineering.
Afin de rendre le processus de préparation des commandes et de supplémentation des matériaux aussi efficace que possible, des convoyeurs à rouleaux et des élévateurs continus ont été installés pour amener les bacs aux employés. De cette façon, le temps est économisé et les employés ne doivent pas parcourir de longues distances inutilement. Les bacs sont automatiquement amenés dans les zones correctes via le système de transport. Le système de transport est utilisé pour les produits entrants et sortants. Les bacs vides remontent via l'ascenseur continu.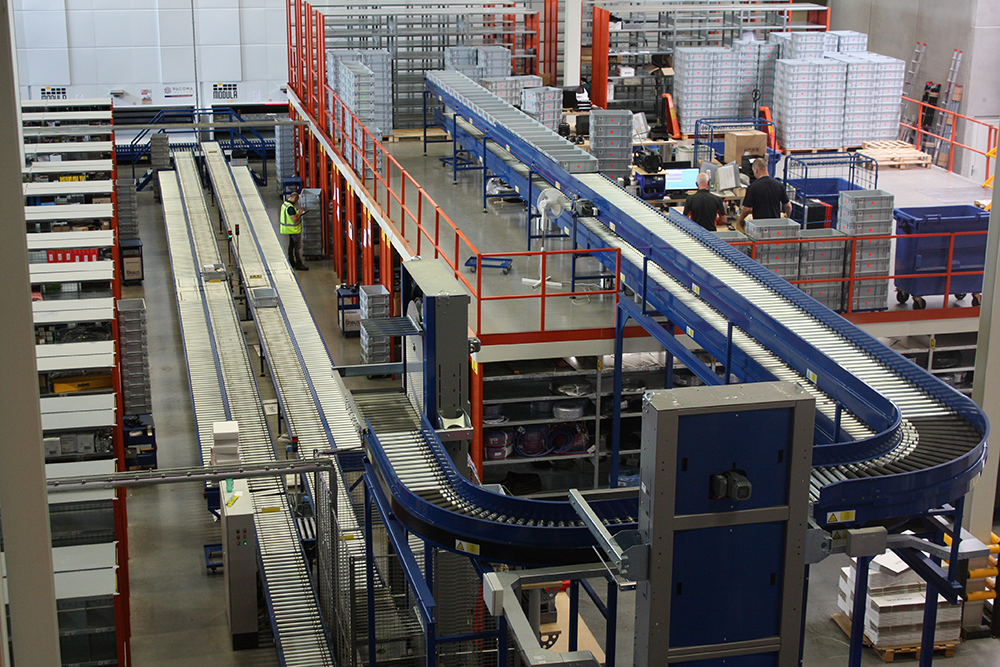
Les processus entrants et sortants sont donc confus. Alors que Bus continuait de croître, les processus entrants et sortants ont de nouveau été séparés dans une deuxième phase. Pour optimiser le processus, une mezzanine a été construite avec des ascenseurs continus et une section supplémentaire de convoyeur à rouleaux. Les marchandises sont reçues sur la mezzanine et réparties dans les bacs entrants. Celles-ci passent par les ascenseurs continus et les convoyeurs à rouleaux jusqu'aux zones correctes. Les bacs sortants se déplacent avec les convoyeurs à rouleaux et traversent toutes les zones de prélèvement et finissent par se retrouver dans six lignes d'emballage. Là, les bacs sortants sont automatiquement distribués dans la bonne zone d'emballage.
Pour stocker les petits matériaux sur la plus petite surface possible, 4 lifts Modula de 10 mètres de haut ont été installés dans le magasin. Cela permet non seulement d'économiser de l'espace, mais la préparation des commandes est beaucoup plus rapide que lorsqu'ils doivent trouver manuellement les produits des racks. Grâce aux quatre tours de stockage, un seul employé est nécessaire pour récupérer le matériel. Les lifts Modula fonctionnent également avec un système où un nouveau plateau avec du matériel est déjà prête pendant qu'ils travaillent dans le premier plateau. De cette façon, le processus peut s'exécuter deux fois plus rapidement et jusqu'à 400 lignes de commande par magasinier peuvent être traitées par heure.
Les lifts Modula sont contrôlés avec le logiciel Gigasoft.Extended de Vanas Engineering, donc peu d'erreurs peuvent être commises. Par exemple, un pointeur laser dans les tours de stockage indique toujours quel produit doit être collecté. Grâce au système pick-to-light, le bac dans lequel ce produit doit être placé est alors indiqué. Lorsque tous les produits nécessaires ont été collectés, la lampe devient verte et le bac peut se déplacer vers les zones suivantes. Une bande LED au-dessus des plateaux de l'ascenseur Modula indique également si un produit doit être collecté ou complété. Avec une simple indication «in» et «out», il peut être complété et collecté simultanément. Avec ce processus, c’est presque impossible de faire des erreurs.
La préparation par lots est utilisée pour travailler encore plus efficacement. Les bacs sont traités par 5 chez la tour de stockage. Lorsqu'un certain plateau est proposé, il se peut qu'il contienne des produits pour plusieurs bacs. Parce que 5 bacs peuvent être traités en même temps, le plateau n'a pas besoin d'être retournée inutilement et rappelée. De cette façon, les commandes peuvent être traitées de manière encore plus efficace et plus rapide.
Les matériaux plus grands sont stockés dans des rayonnages à tablettes et rayonnages à palettes de META. Ceux-ci sont en partie transportés dans des bacs et en partie collectés manuellement car ils sont trop grands pour les bacs sur les convoyeurs à rouleaux. Les produits inflammables sont stockés sur des rayonnage dans une partie du magasin qui peut être fermée en cas d'incendie. Les plus petites pièces qui passent souvent au comptoir sont stockées à l'avant de la salle d'exposition dans des armoires à tiroirs de Lista.
Parce que Bus Industrial Tools a connu l'efficacité des ascenseurs Modula en combinaison avec les convoyeurs à rouleaux, ils ont déjà fourni de l'espace pour des tours de stockage supplémentaires pour pouvoir stocker encore plus de matériel et pour que leur processus se déroule plus facilement.
Gain d’espace:
Les 4 lifts Modula occupent seulement 66,5 m² de surface au sol. Mais grâce à leur hauteur de 10 mètres, 20 000 emplacements avec différents produits peuvent être traités dans les tours de stockage.
Grâce à la mezzanine et aux ascenseurs des convoyeurs à rouleaux, les marchandises entrantes sont reçues à l'étage. Par conséquent, aucune surface au sol supplémentaire ne doit être prévue au rez-de-chaussée.
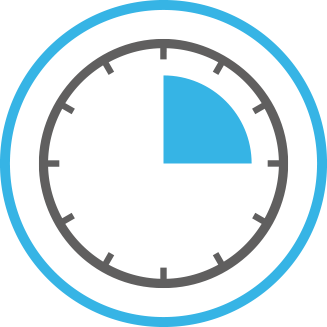
Vitesse:
Le poste externe double permet au système de préparer un deuxième tiroir pendant que l'employé continue de collecté. Ensuite, ils peuvent rapidement changer de tiroir et travailler deux fois plus vite. Aux heures de pointe, les employés peuvent traiter jusqu'à 400 lignes par heure par employé avec les tours de stockage.
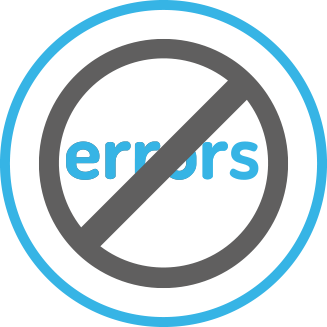
0% de fautes:
Plus d'erreurs ne sont commises par les outils supplémentaires tels que le pointeur laser, la barre LED et le système pick-to-light.
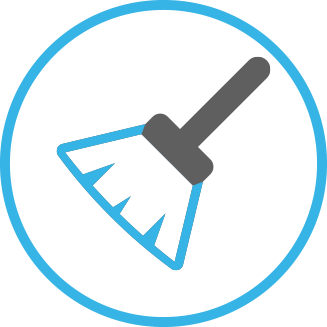
Stockage sans poussière:
Les produits restent soigneusement rangés dans les tours de stockage et n'ont plus besoin d'être dépoussiérés.
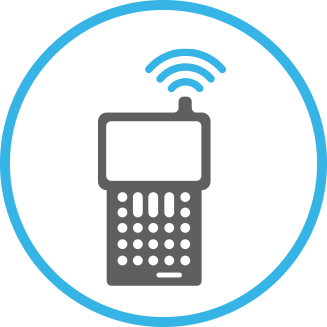
Administration simplifée:
Toutes les manipulations sont renvoyées en temps réel. Gigasoft.Extended, qui est lié au WMS global d'Actemium, fournit une gestion complète au sein de la tour de stockage.
Ergonomie:
Les produits sont toujours proposés à une hauteur ergonomique dans les tours de stockage et les convoyeurs. De plus, les employés n'ont pas à parcourir des distances inutiles car les bacs sont amenés dans leur zone grâce aux convoyeurs à rouleaux.
INSTALLATION:
- 4 lifts Modula d’une hauteur de 10 mètres
- Chaque tour de stockage dispose d'un double poste de travail externe
- Chaque tour de stockage a une barre LED graphique et un panneau de commande mobile
- Chaque tour de stockage dispose d’un pointeur laser
- Système Pick-to-light
- Système de convoyeur à rouleaux
- 2 ascenseurs continus
- Rayonnages à tablettes
- Rayonnages à palettes
- Armoires à tiroirs Lista
LOGICIEL:
- Gigasoft.extended lié avec le WMS d’Actemium
- Module de gestion automatique des emplacements
Découvrez toutes nos solutions d’équipement de magasins ici.